X-ray machines play a pivotal role in various fields, facilitating critical diagnostics and aiding in medical, industrial, and scientific endeavors. The reliable operation of these machines is paramount, and efficient troubleshooting and diagnosis are essential to maintain their optimal functionality. This guide delves into the systematic process of identifying and resolving issues that may arise with X-ray machines. By following the informative steps outlined in this guide, technicians and operators can navigate the complexities of X-ray machine maintenance with professionalism and expertise.
I. Common Technical Issues and Error Codes
A. Understanding Error Codes
- Error codes serve as invaluable diagnostic tools, providing insights into potential malfunctions within the X-ray machine.
- It is crucial to consult the machine's manual, which contains a comprehensive list of error codes along with their corresponding explanations.
B. Power and Connectivity Issues
- When faced with power-related problems, a systematic approach to troubleshooting is essential.
- Begin by examining power cords, ensuring proper connections to outlets and power sources.
C. Calibration and Alignment Problems
- Misalignment within an X-ray machine can significantly impact image quality and overall performance.
- Recalibration and realignment of machine components are necessary steps to restore accurate functionality.
D. Mechanical Malfunctions
- Moving parts and mechanical components can be susceptible to malfunctions over time.
- Regular maintenance tasks such as lubrication, cleaning, and preventive measures are essential to address these issues effectively.
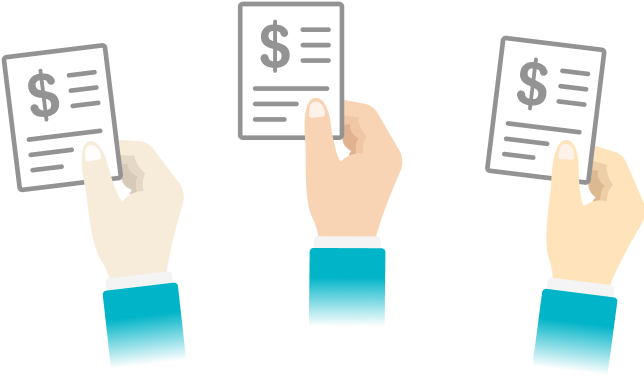
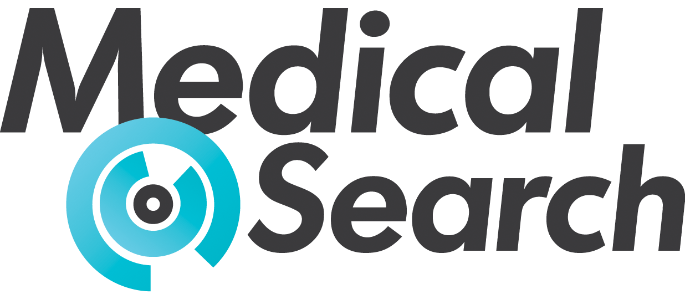
Find the right X-Ray Machine
Compare quotes from expert Australian suppliers and make the best choice. It's free, quick and easy!
II. Steps for Identifying Malfunctioning Components
To maintain the optimal functionality of an X-ray machine, timely and accurate diagnosis of potential issues is imperative. This section outlines a systematic approach to identifying malfunctioning components, ensuring that the X-ray machine remains in peak operational condition. The steps detailed below, comprising visual inspection, systematic testing, and diagnostic imaging, collectively form a comprehensive strategy for effectively diagnosing X-ray machine problems.
A. Visual Inspection
- Importance of External Examination for Physical Damage:
The first step in troubleshooting an X-ray machine involves a meticulous visual inspection of its external components. This process is essential to detect any visible physical damage, wear, or abnormalities. Scrutinizing the machine's exterior provides initial insights into potential issues that might affect its performance. Timely identification of physical damage allows for prompt repair or replacement, preventing more significant problems down the line.
- Checking for Loose Connections or Detached Components:
Loose connections and detached components can lead to operational inefficiencies and errors in X-ray imaging. During the visual inspection, pay close attention to cable connections, connectors, and fasteners. Securely fastened components ensure stable electrical and mechanical connections, minimizing the risk of disruptions. Addressing loose connections early not only enhances functionality but also prevents potential safety hazards.
B. Systematic Testing
- Using a Systematic Approach to Isolate Faulty Parts:
When a malfunction is suspected, a systematic testing approach is indispensable. This method involves dividing the X-ray machine into manageable sections and testing each part individually. By isolating specific components, it becomes easier to pinpoint the source of the problem. This systematic approach streamlines the diagnostic process, expediting repairs and minimizing downtime.
- Verifying the Functionality of Critical Components:
Critical components, such as the X-ray tube, generator, and imaging receptors, play pivotal roles in the machine's performance. Each of these components must undergo thorough functional testing. This verification process involves conducting diagnostic tests and using precision instruments to assess the functionality of these critical elements. Identifying potential issues with these components ensures accurate diagnoses and effective repairs.
C. Diagnostic Imaging
- Employing Test Images to Identify Irregularities:
Diagnostic imaging forms a cornerstone of X-ray machine troubleshooting. By capturing and analyzing test images, you can identify irregularities and deviations from the expected results. Comparative analysis of test images against reference images assists in identifying subtle changes in image quality, alignment, or calibration. This step is crucial in diagnosing issues that might not be apparent during visual inspection.
- Analyzing Images for Artifacts, Inconsistencies, and Distortions:
Analyzing diagnostic images goes beyond identifying irregularities; it includes detecting artifacts, inconsistencies, and distortions in the images produced. Artifacts can stem from a variety of sources, such as mechanical errors or software glitches. Rigorous image analysis aids in understanding the nature of these artifacts and helps direct the diagnostic process towards their root causes.
III. Diagnosing Image Quality Problems and Artifacts
Modern X-ray machines play a crucial role in various fields, including healthcare and industrial applications, where accurate imaging is essential for diagnosis and analysis. Ensuring optimal image quality is paramount, and any artifacts or issues that compromise it can significantly impact the utility of these machines. In this section, we delve into the process of diagnosing image quality problems and artifacts that can arise during X-ray imaging. The approach is rooted in a technical understanding of the machines' components and their interaction with imaging processes.
A. Image Artifacts: Causes and Solutions
- Common Artifacts and Their Underlying Causes: Artifacts are unintended anomalies present in X-ray images that can obscure critical details and distort information. Common artifacts include streaks, shadows, and blurriness. These artifacts can stem from various sources, such as patient movement, equipment malfunctions, or improper calibration. For instance, streak artifacts may result from faulty detector elements, while shadows might occur due to improper X-ray beam alignment. Identifying the source of each artifact is crucial to implementing effective solutions.
- Techniques to Minimize or Eliminate Artifacts: Addressing artifacts necessitates a systematic approach. Ensuring proper patient positioning, minimizing motion during exposure, and employing immobilization techniques can mitigate artifacts caused by patient movement. Regular maintenance and calibration checks can rectify artifacts tied to equipment malfunctions. Additionally, optimizing exposure settings and fine-tuning image processing algorithms can help reduce noise and enhance overall image quality.
B. Image Quality Parameters
- Explaining Factors Affecting Image Clarity and Detail: Achieving optimal image quality depends on a combination of factors. X-ray beam energy, exposure time, and detector resolution collectively impact image clarity and detail. A higher-energy X-ray beam can penetrate dense structures more effectively, while longer exposure times capture finer details. Detector resolution determines the level of detail discernible in the final image.
- Adjusting Parameters for Optimal Image Quality: Radiologic technologists and operators must understand the interplay of parameters to achieve the desired image quality. The appropriate balance between X-ray energy, exposure time, and detector settings should be maintained. Moreover, adjustments to patient positioning and alignment of the X-ray machine can further enhance image quality. Regular training and skill development for operators are imperative to ensure consistent and high-quality images.
C. Software-Related Issues
- Addressing Software Glitches Affecting Image Output: X-ray machines often rely on intricate software systems for image processing and enhancement. Software glitches can lead to inconsistent image output, including incorrect brightness and contrast levels or even complete image corruption. Such issues might arise due to coding errors, compatibility problems, or software degradation over time.
- Reinstalling Software or Applying Updates as Necessary: Resolving software-related problems involves a combination of diagnostics and solutions. In some cases, reinstalling the software to its original state might rectify minor glitches. Additionally, software updates released by the manufacturer can address known issues and introduce optimizations. Regularly updating and maintaining software integrity is essential for consistent image quality and the overall functionality of the X-ray machine.
IV. Utilizing Diagnostic Tools and Equipment for Assessment
In the realm of maintaining optimal functionality and performance of X-ray machines, the utilization of diagnostic tools and equipment holds paramount significance. This section delves into the crucial role these tools play in facilitating precise assessments, offering valuable insights, and ensuring accurate diagnoses of potential issues. By shedding light on the importance of diagnostic tools, discussing various testing instruments, and exploring the utility of imaging analysis software, this section equips readers with essential knowledge for effective troubleshooting and diagnostics.
A. Importance of Diagnostic Tools
- Highlighting Specialized Tools for Precise Diagnosis: Diagnostic tools tailored to the intricacies of X-ray machines are indispensable assets for technicians and engineers. These tools are meticulously designed to pinpoint specific issues within the intricate machinery, enabling professionals to identify root causes accurately. By utilizing these specialized tools, professionals can streamline the diagnosis process, minimize downtime, and expedite repairs, ultimately enhancing the overall operational efficiency of X-ray machines.
- Discussing Benefits of Using Appropriate Tools: The benefits of employing the right diagnostic tools are manifold. First and foremost, these tools enhance accuracy by providing quantitative measurements and data, which serve as objective bases for assessment. Additionally, these tools facilitate a systematic approach to diagnostics, ensuring comprehensive coverage of potential problem areas. This, in turn, prevents misdiagnoses and the unnecessary replacement of functional components. The judicious use of diagnostic tools not only saves valuable time but also contributes to cost-efficiency by minimizing trial-and-error approaches.
B. Testing Instruments
- Overview of Tools for Measuring Radiation Output and Quality:
Accurate measurement of radiation output and quality is fundamental to the performance of X-ray machines. Testing instruments such as dosimeters, sensors, and gauges are designed to quantify radiation levels, ensuring compliance with safety standards and accurate diagnostic imaging. Dosimeters enable the measurement of radiation exposure over time, while sensors provide real-time feedback during X-ray procedures. Gauges, on the other hand, assess the consistency and uniformity of radiation distribution, crucial for obtaining high-quality images.
- Proper Usage of Dosimeters, Sensors, and Gauges:
Professionals must adhere to proper usage guidelines for testing instruments to ensure accurate results. Dosimeters should be calibrated and positioned correctly to measure radiation accurately. Sensors must be positioned in proximity to the X-ray beam's target area to provide immediate feedback. Gauges demand meticulous placement to evaluate radiation uniformity across the imaging field. By adhering to usage protocols, technicians can obtain reliable data for assessing radiation levels and quality.
C. Imaging Analysis Software
- Utilizing Software for In-Depth Image Analysis:
Imaging analysis software complements the hardware-focused diagnostic tools by delving into the quality and characteristics of X-ray images. This software allows professionals to scrutinize image parameters such as contrast, brightness, and resolution, revealing subtle deviations from the expected norms. Such in-depth analysis aids in identifying issues that might not be immediately apparent to the naked eye, ensuring comprehensive assessments.
- Extracting Valuable Insights from Image Data:
Imaging analysis software enables the extraction of quantitative data from X-ray images, facilitating a data-driven approach to diagnostics. By quantifying image attributes, professionals can establish benchmarks for image quality and track deviations over time. This quantitative analysis aids in trend identification, enabling proactive maintenance and troubleshooting. Moreover, software-generated reports provide clear documentation of image quality, aiding in collaboration with technical support and decision-making.
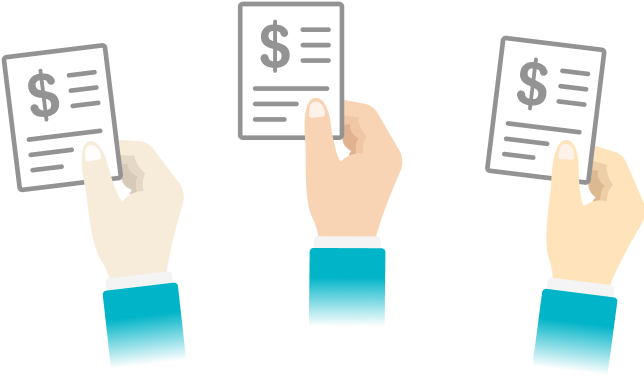
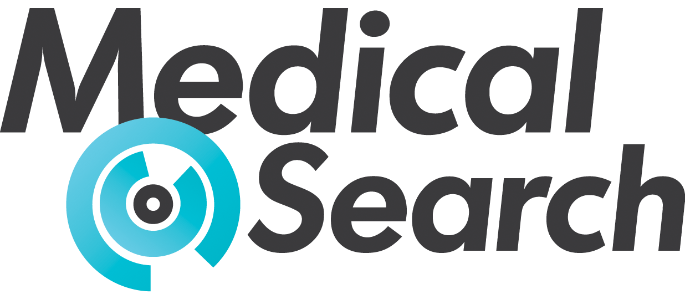
Find the right X-Ray Machine
Compare quotes from expert Australian suppliers and make the best choice. It's free, quick and easy!
V. Collaborating with Technical Support or Service Professionals
A. Knowing When to Seek Help
- Indicators of Issues Beyond On-Site Troubleshooting
When encountering persistent technical problems with your X-ray machine, it's crucial to recognize signs that go beyond the scope of on-site troubleshooting. These indicators include:
- Repeated recurrence of the same issue despite attempted solutions.
- Unusual or alarming noises during machine operation.
- Drastic deterioration in image quality with no identifiable cause.
- Error codes or malfunctions that persist after following recommended steps.
- Recognizing Situations Requiring Expert Intervention
Certain situations warrant the expertise of technical support or service professionals:
- Complex errors or error codes that require specialized knowledge to decipher.
- Mechanical failures that involve intricate components or delicate adjustments.
- Calibration or alignment issues that demand precision and in-depth technical knowledge.
- Suspected software or firmware problems that affect multiple aspects of machine functionality.
B. Effective Communication with Support
- Articulating Observed Issues and Steps Taken
When communicating with technical support or service professionals, clear and concise communication is paramount. Provide a comprehensive description of the observed issues, including:
- Specific error codes displayed, if applicable.
- Detailed account of any changes or incidents leading up to the problem.
- A chronology of the steps you've taken to troubleshoot and resolve the issue.
- Providing Accurate Information for Efficient Remote Assistance
For remote assistance to be effective, accurate information is essential. Ensure you:
- Specify the model and serial number of the X-ray machine.
- Detail any recent maintenance or repairs conducted on the machine.
- Share relevant diagnostic images or logs, if available.
- Confirm the version of software or firmware currently installed.
C. Service Agreement Considerations
- Discussing Benefits of Service Agreements
Service agreements offer valuable benefits for maintaining your X-ray machine's functionality and reliability. These advantages include:
- Regular preventive maintenance to minimize potential issues.
- Timely access to technical support for swift issue resolution.
- Priority response times for urgent problems.
- Cost-effective solutions for unexpected repairs.
- Understanding Terms, Response Times, and Coverage
- Prior to entering into a service agreement, it's crucial to comprehend the terms and conditions:
- Review response time commitments for different types of issues.
- Understand the extent of coverage, including parts and labor.
- Clarify the procedures for scheduling maintenance visits or technical support interactions.
- Inquire about options for extending or customizing the service agreement to match your specific needs.
In conclusion, troubleshooting and diagnosing issues with X-ray machines is a critical skill for technicians and operators to ensure their optimal functionality. This guide has outlined a systematic approach to identifying and resolving common technical issues and error codes, including power and connectivity problems, calibration and alignment issues, and mechanical malfunctions. It has emphasized the importance of visual inspection, systematic testing, and diagnostic imaging in the process of identifying malfunctioning components.